Glass Production: From Raw Materials to Finished Products
Glass is a versatile and essential material used in various industries and everyday applications. From windows and bottles to electronics and automotive components, glass plays a significant role in our lives. Have you ever wondered how glass is produced, starting from raw materials and ending with the finished products we use? This article takes you on a journey through the glass production process, exploring the steps involved and the key factors that contribute to the quality and characteristics of the final glass products.
- Raw Materials:
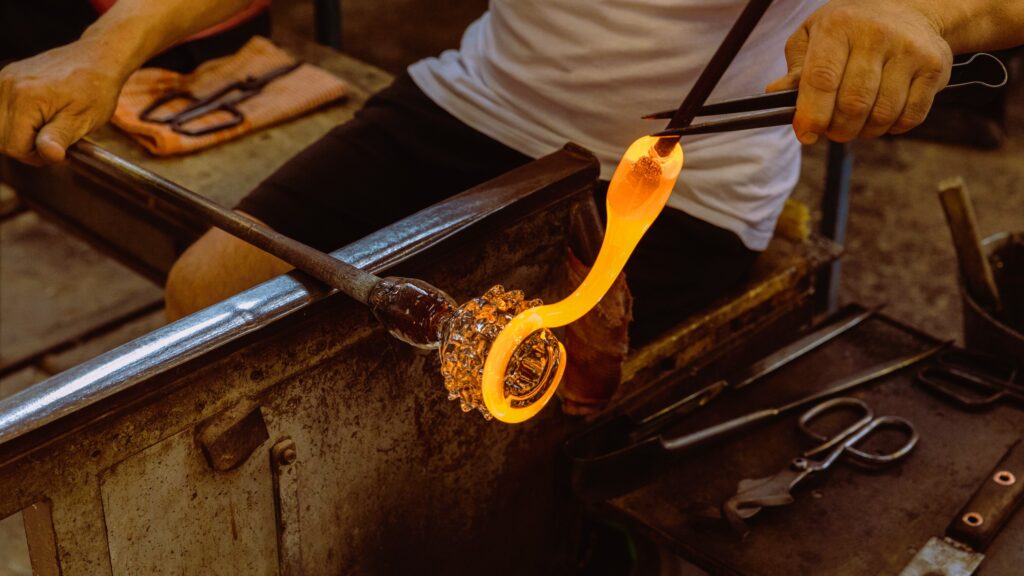
The production of glass begins with carefully selected raw materials. The primary ingredients used in glass production are silica sand, soda ash, and limestone. These materials are blended in specific proportions to form a glass batch. Silica sand provides the necessary silicon dioxide (SiO2) content, soda ash acts as a flux to lower the melting point, and limestone helps stabilize the mixture.
- Batch Preparation:
Once the raw materials are obtained, they undergo a series of processes to create the glass batch. The materials are carefully measured and mixed in large furnaces. This mixture is then heated to high temperatures, typically above 1500°C, in order to melt and fuse the components together. The resulting molten glass is a crucial intermediate stage in the glass production process.
- Glass Forming:
After the glass batch is melted, it is ready to be shaped into the desired form. There are several methods of glass forming, including blowing, pressing, and drawing. Glass blowing involves gathering molten glass on the end of a blowpipe and shaping it by blowing air into it. Pressing is used to create glass objects with intricate designs by pressing the molten glass into a mold. Drawing is the process of pulling molten glass through dies to form thin sheets or fibers.
- Annealing and Tempering:
To ensure the durability and strength of glass products, the formed glass undergoes annealing and tempering processes. Annealing involves controlled cooling of the glass to relieve internal stresses, making it less prone to cracking or breaking. Tempering, on the other hand, involves subjecting the glass to high heat followed by rapid cooling to create a stronger, shatter-resistant product.
- Finishing and Quality Control:
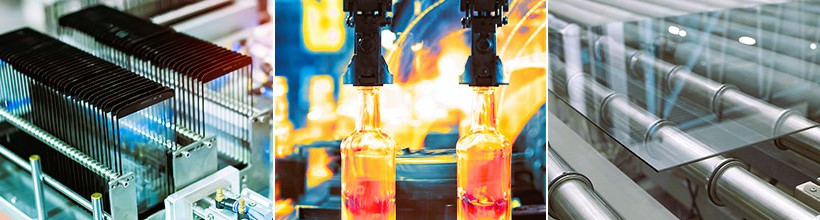
Once the glass has been formed and treated, it undergoes various finishing processes to achieve the desired characteristics. This may include cutting, grinding, polishing, and coating the glass surface. Additionally, rigorous quality control measures are implemented to ensure that the glass products meet industry standards and customer requirements. These measures include testing for strength, transparency, chemical resistance, and other specific properties.
Conclusion:
The process of glass production is a complex and precise undertaking, involving the careful selection and preparation of raw materials, the controlled melting and forming of glass, and the application of finishing touches. The quality and characteristics of glass products depend on factors such as the composition of raw materials, the manufacturing techniques employed, and adherence to established standards and regulations.